5 Key Factors in Industry 4.0: The Game Changer for Manufacturers in 2022
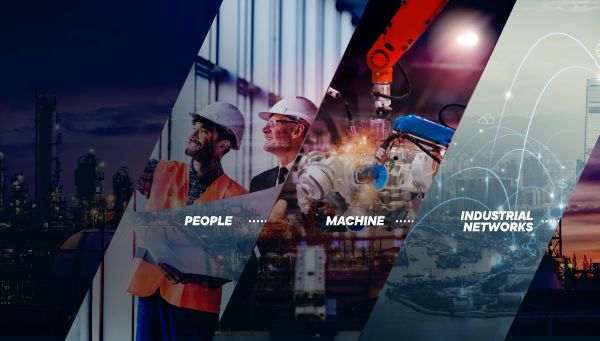
The 4th industrial revolution ushers every Industry into immense transformations, with enormous advantages and implementation challenges. The goal of Industry 4.0 is to integrate physical and digital technologies into a cyber-physical system (CPS) that reflects the digital world in the physical world and vice versa; in addition to that, it also enhances the customer experience. For organizations, implementing Industry 4.0 is a daunting challenge. The process starts with understanding the existing workflow of the business, identifying the bottlenecks, and selecting the right technologies to overcome the workflow and business problems. In order to make this process simpler, our research team and industry experts suggested 5-key factors that help organizations implement Industry 4.0 with fewer complications and faster success.
5 Key Factors- Effective ways to implement Industry 4.0 in your organization
There are numerous factors that organizations ought to consider in order to embrace Industry 4.0 successfully. However, here are the five most essential factors that help shape Industry 4.0 at its core and make the implementation process hassle-free. When integrated, each of these pieces create a capability that can help in bringing transformation.
1. Identifying and Implementing Right Technologies
Customer-centric technologies have enabled OT IT Convergence, highly recommended to manufacturers, mandating them to integrate their IT (Information Technology) and OT (Operational Technology) and transform real-time data into actionable intelligence. Enterprise information technology must securely collect data from OT equipment before processing it and sharing the necessary insights with OT professionals and other internal and external stakeholders to maximize IIoT project return on investment (ROI).
By Integrating OT Plant Data with IT Systems such as ERP, WMS, and other third-party IT suites, whether on-premises or in the cloud, there would be clear shop floor data visibility by integrating Computerized Maintenance Management Systems (CMMS) with a SCADA system, Cloud/Edge-based Remote Monitoring Solutions with these operations.
The next point to mention is that AI (Artificial Intelligence) brings flexibility to adapt various technologies that enable software and machines to perceive, comprehend, act, and learn independently or to augment human operations.
Industrial production can be more convenient than manual processes by incorporating artificial intelligence. These technologies offer vast potential for manufacturing companies to work even faster and more flexibly, which helps achieve the best possible quality while cutting down on the resources used and driving greater production efficiencies.
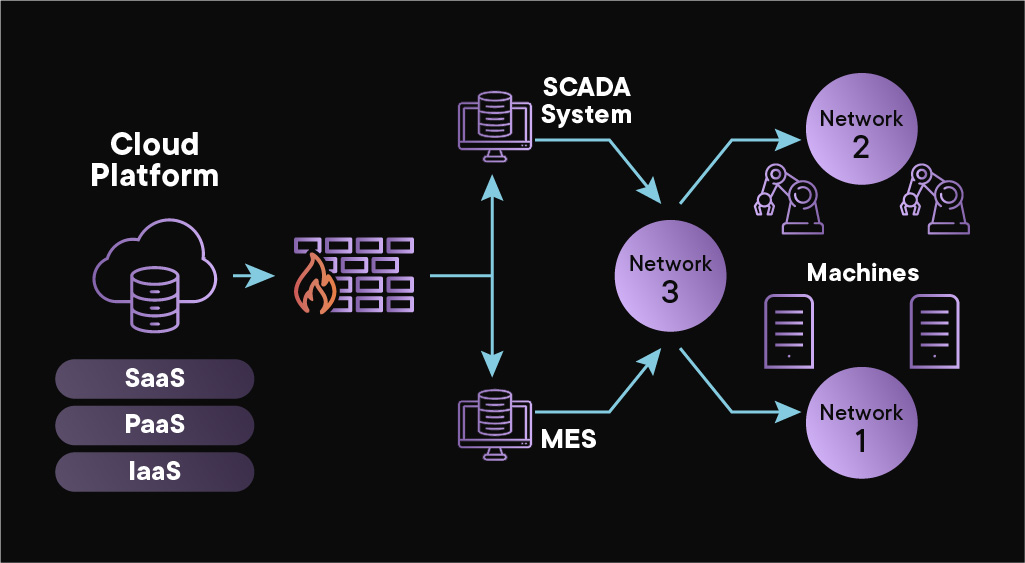
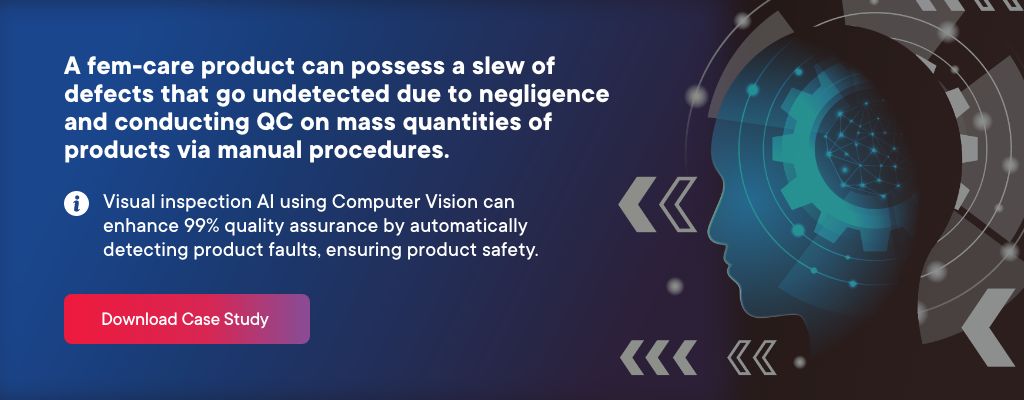
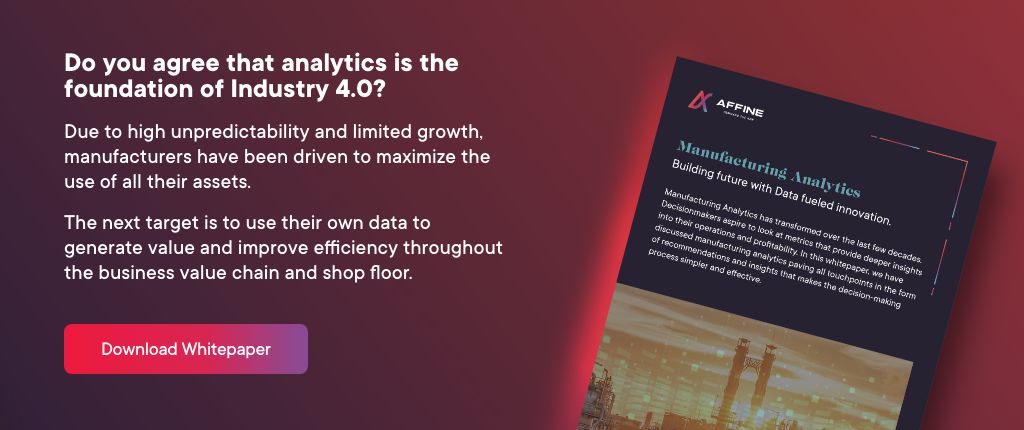
2. Selecting The Right Use Case for Your Need
When a new technology is introduced, the scope and significance of its advantages are usually unclear until after it is put to use. Early IIoT adopters and digital transformation pioneers served as role models for other sectors who were always interested in exploring the new avenues offered by emerging technologies. It takes a particular vision to apply use cases to a different business, but it eliminates the risk of buying on trust.
Use cases are just the beginning, and the idea is to learn about what others have done or are doing and seek techniques to make the outcomes they’re getting relevant to your business. The first approach is to understand why the company is still attempting to figure out its IIoT strategy and needs to build a list of problem statements planning to resolve. The next step is to look to peer companies, research analysts, and solution providers’ case studies to understand digital transformation use cases, entry points, techniques, and rewards. Start with a PoC having low resources, low effort, and high impact; when the results are visible, start implementing use case simultaneously following the same strategy.
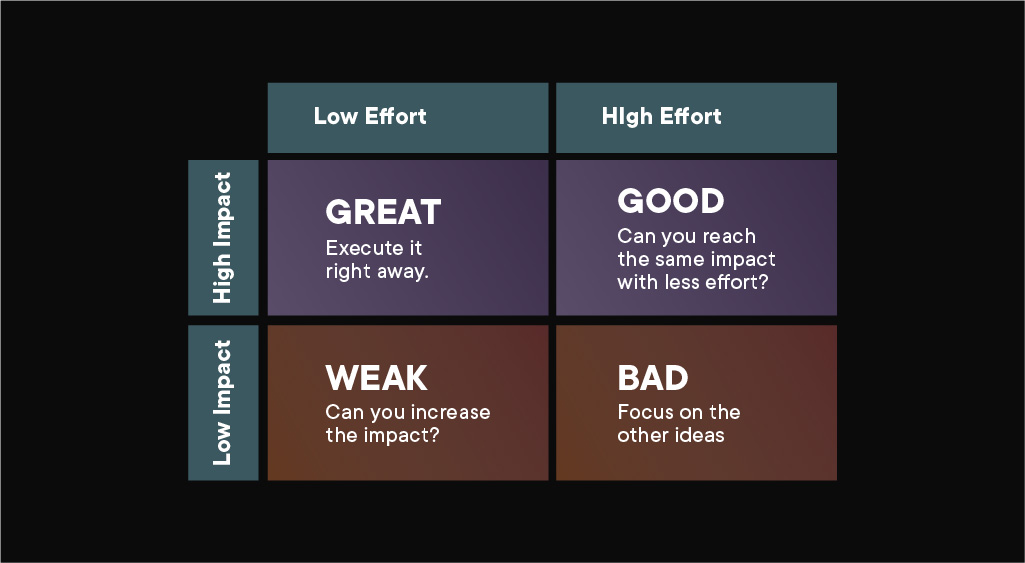
Few use cases offered by Affine for different functions:
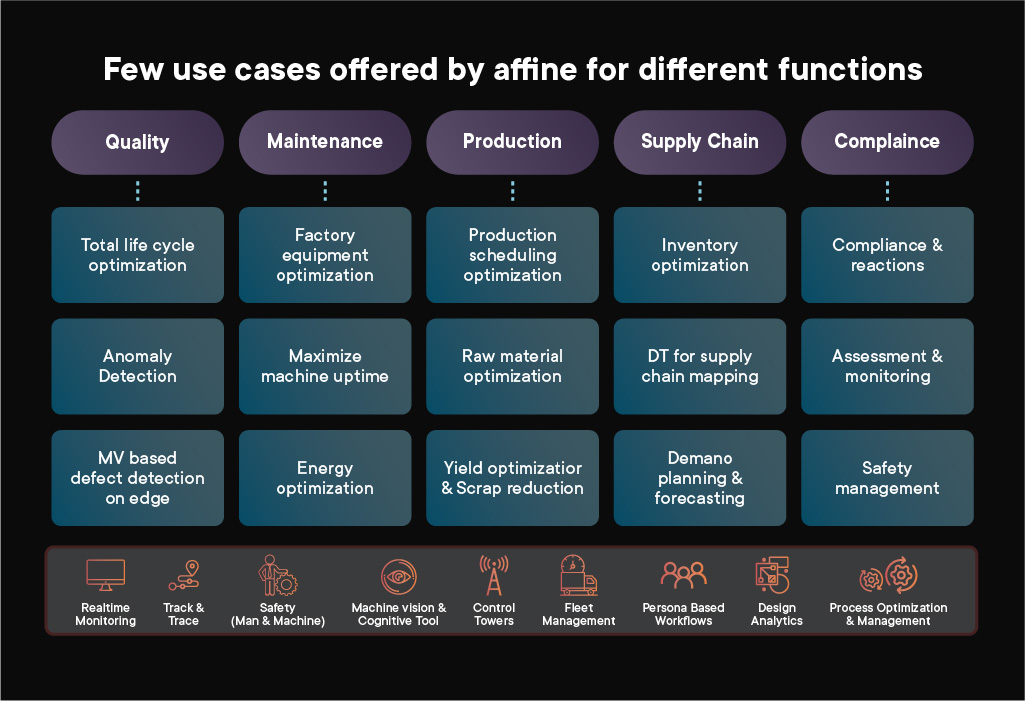
3. Identifying the skill gap, filling it with right skillsets
Organizations are recognizing IoT in the paradigm of a highly autonomous production line to envision all of the skills that are required to implement Industry 4.0. It could comprise additive manufacturing techniques, CNC lathes, and newer machines capable of executing highly variable, multi-step processes with the help of robotic vision, artificial intelligence, and cobots that work alongside humans. We now have a technology landscape that requires multiple skill sets and the blending of those skills to cut across silos and unique skills to create entirely new categories of technology professionals—those who understand the convergence of operational and information technologies.
Now is the time to think cross-discipline or multi-discipline. People claim the Internet of Things is about digitizing things when they talk about them. It’s all about digitizing business processes. As a result, engineers, network specialists, application developers, prominent data architects, UI [user interface] designers, and businesspeople must communicate and comprehend each other. Industry 4.0 will necessitate the organization of multidisciplinary teams to solve complex challenges. Of course, specialists will be required, but they will also need to broaden their knowledge to cover other IT technologies like cloud, AI, analytics, and operational technologies such as robotics and process automation that keep factories and assembly lines operating. To do so, train the people, develop continuous learning programs as a regular practice, hire people with good knowledge who are needed to bridge the gap, and have new people on board to help cross-learn and motivate the team. This is to unlock their potential to create a sustainable workplace.
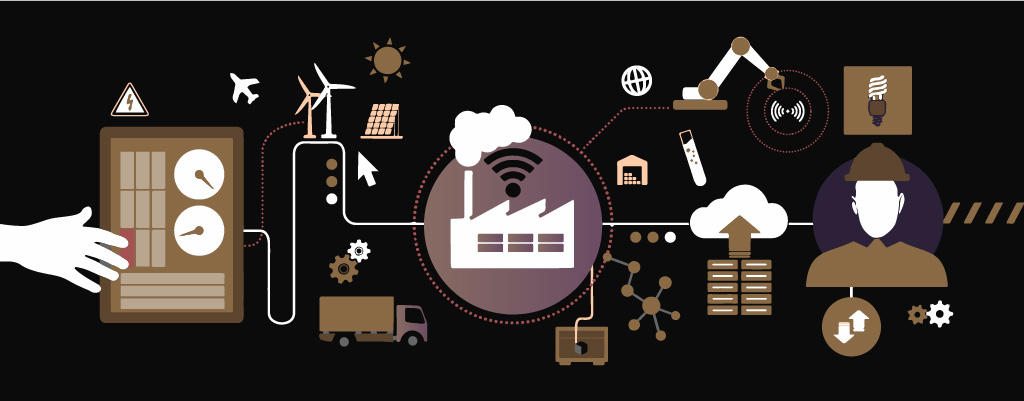
4. Change Your Vision and Transform Your Company Culture
The force behind the “Digital Transformation” has become an extensive expression used across several industries and contexts to describe the process through which a company adopts and implements digital solutions that benefit its activities. It is crucial to notice the narrative around digital transformation as it enables a cultural shift in the company. Remarkably, how often do we discuss culture as a consequence of an event rather than as the driving force behind it? This approach may still be missing in some essential aspects.
The advantage of a digital tool, no matter how good it is or what benefits it offers, will be lost if the company is not prepared to handle it. The project’s true potential is hidden, resources are wasted, and it is on the brink of failure. Aligning business with right operational practices denote the company culture, key factors that facilitate digital transformation approach to drive cultural change, and shop floor employees’ engagement with the vision and road map makes it simple. This transparent process guides CDOs and digital leaders. As organizations prepare for and impose digital transformations, it is crucial to promote a culture where everybody is tech-savvy, and security is everyone’s consideration.

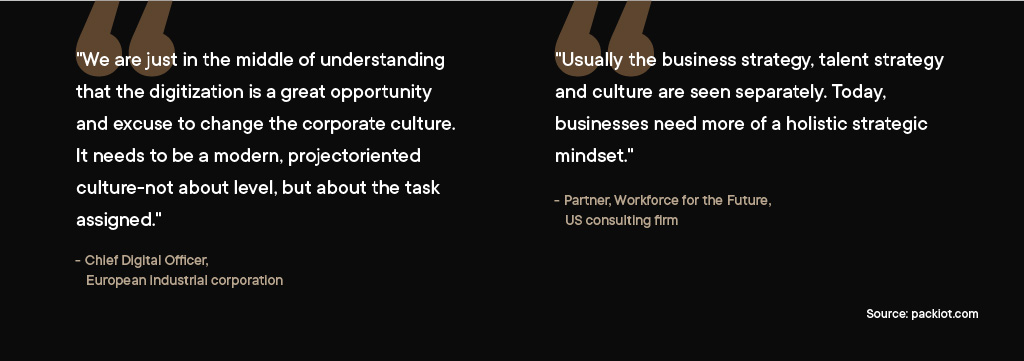
5. Finding the Right Partners/Vendors
Plan the scope of your business and align your goals with the company’s general strategy by selecting that the right vendor/partner for implementing the IR 4.0 applications plays a pivotal role. Start with pilot projects, validate results, and systematize the learning mechanisms initially to understand the scope aligned with your requirements. To achieve this, model projects and “best practices” should be promoted and invest in a digital learning technique.
Whether they recognize it or not, most production managers today are already in a race. It’s a culture to adapt and implement new manufacturing systems and technologies; as we all know, integration and collaboration are at the core of Industry 4.0. Create a strategy before embarking on a long journey without a map, and you should do the same with Industry 4.0 adoption. This is a crucial step in the procedure. Once you’ve determined your desired maturity level, you’ll need to create a thorough implementation strategy to assist you in achieving your objectives.
A potential and effective partner will monitor your current functioning, detect traps, comprehend obstacles, and provide a healthy way to proceed or a new course of action. Ultimately, this will solve your existing challenges and assist you in generating new value from them. In the usual approach, they should give you a road plan for pushing your business to the next level. And they should let you comprehend it in a logical fashion without a slew of technical jargon.
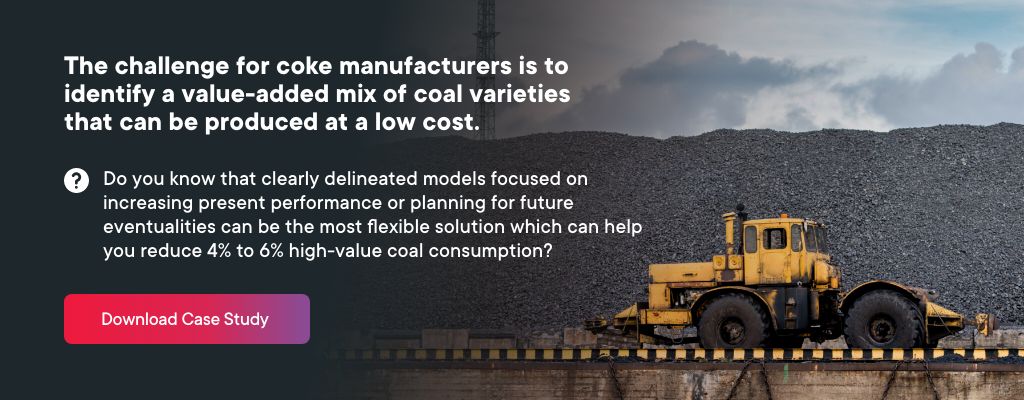
Conclusion
Manufacturers and the manufacturing industry as a whole are seeking direction as we approach 2022, not least due to the ongoing global COVID-19 pandemic. However, the last few years have given us much learning that signifies resilience, innovation, and the sector’s ability to persevere in the face of adversity.
There are numerous opportunities for all industrial sectors, ranging from acquiring fresh talent to exploiting data more effectively to contribute to a more sustainable world. Smart Manufacturing and Industry 4.0 solutions and efforts will always be vital in manufacturing and many other sectors.
Are you looking to know how your industry will change in the era of Industry 4.0 and want to be a winner in this new world? Listen to our industry leaders and experts and ask your questions at our virtual event on “Demystifying Industry 4.0”. Our speakers are sharing real-life use cases and insights into opportunities that are driving their growth and success with Industry 4.0. Go ahead, Register Now – this is going to be a great event!
Stay tuned for more information!