Top 5 Challenges- Implementing Industry 4.0!
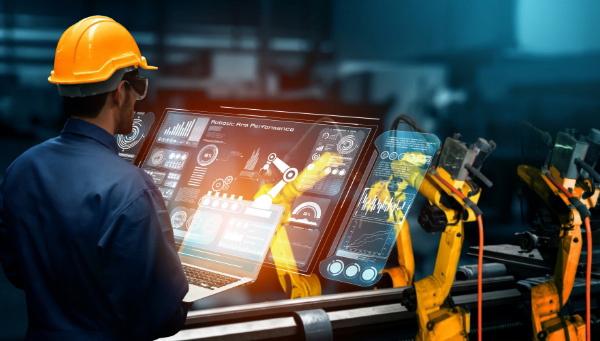
Today, the entire world is grappling with the COVID-19 pandemic, which has intensified supply chain concerns and prompted many businesses to rethink their sourcing strategies. Several businesses are focusing on localization for two reasons: one, to be closer to the source, and the other, to minimize the risk of disruption.
Well, necessity is the mother of invention, and this is undeniably true for technological innovations, precisely Industry 4.0 solutions. Evolution is the result of real hardship. In the case of manufacturing, the movement of Industry 4.0 is caused by volatile market demands for better and quicker production techniques, shrinking margins, and intense contention among enterprises that is impossible without smart technology.
Smart Manufacturing will be based on digitization and Industry 4.0 and large enterprises are inclining towards digital innovation. However, SME’s and MSMEs are still struggling with several challenges to adopting the Digital Transformation and Industry 4.0 initiatives. These obstacles may dissuade some manufacturing companies from adopting these technologies, causing them to fall behind their peers.
The Top Five Challenges!
SMEs and MSMEs still experience difficulties achieving Industry 4.0 goals, although smart manufacturing is often associated with Industry 4.0 and digital transformation. Here are the five challenges:
1. Organization Culture:
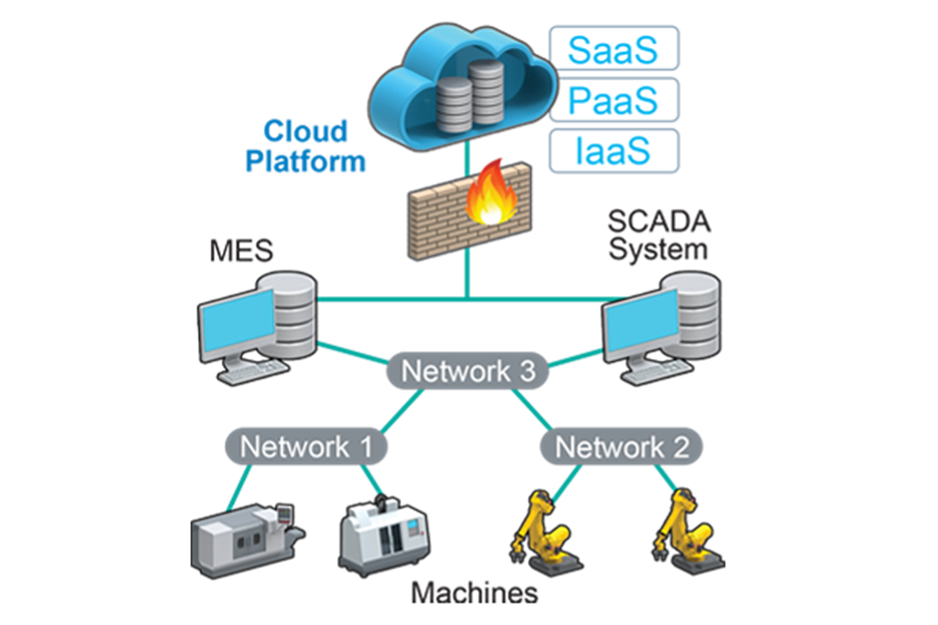
This is one of the immense challenges for any organization to evolve from ad-hoc decisions to data-based decision-making. Part of this is driven by the data availability and the CXO’s awareness and willingness to adopt new Digital technologies. Navigating the balance between culture and technology together is one of the toughest challenges of digital transformation.
2. Data Readiness/Digitization:
Any Digital Revolution succeeds on the availability of data. Unfortunately, this is one of the most significant opportunities for SMEs. Most of the manufacturing plants in SMEs lack basic data capture and storage infrastructure.
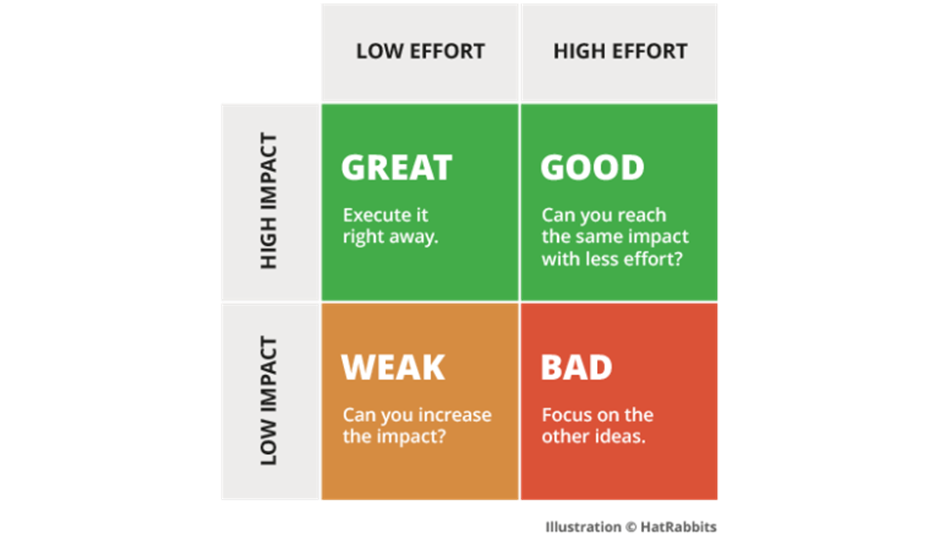
Most places have different PLC protocols (e.g., Siemens, Rockwell, Hitachi, Mitsubishi, etc.), and the entire data is encrypted and locked. This either requires unlocking encryption by the control systems providers or calls for separate sensor or gateway installations. Well, this is a huge added cost, and SMEs have not seen any benefits so far, as they have been running their businesses frugally.
3. Data Standardization and Normalization:
This is a crucial step in the Digital Transformation journey, enabling the data to be used for real-time visibility, benchmarking, and machine learning.
Most SMEs grow in an organic way, and there’s an intent to grow most profitably. Typically, IT and OT technology investments are kept to a bare minimum. As a result, most SMEs are missing SCADA/MES’S systems that integrate the data in a meaningful way and help store it centrally. As a result of missing this middleware, most of the data needs to be sourced from different sensors directly or PLCs and sent via gateways.
All this data cannot be directly consumed for visualization and needs an expensive middleware solution (viz., LIMS (Abbott, Thermo Fischer), and LEDs- GE Proficy); this is again an added cost.
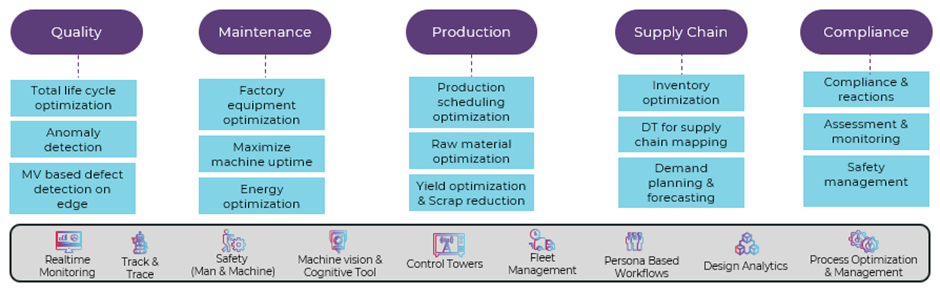
Additionally, the operational data is not all stored in a centralized database. Instead, it is available in real-time from Programmable Logic Controllers (PLCs), machine controllers, Supervisory Control and Data Acquisition (SCADA) systems, and time-series databases throughout the factory. This increases the complexity of data acquisition and storage.
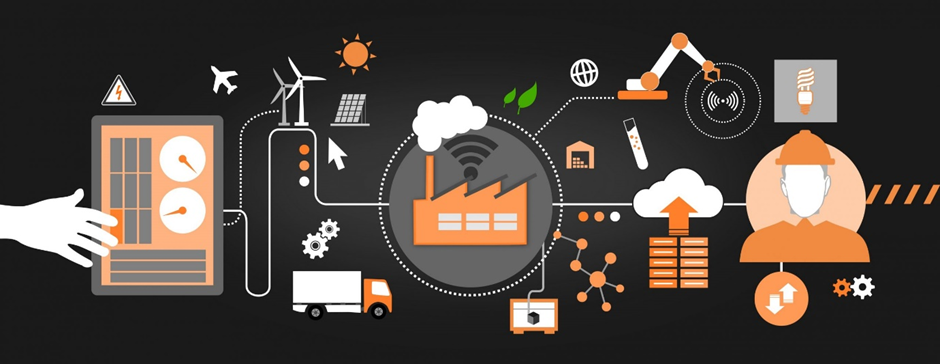
4. Lack of Talent for Digital:
Believe it or not, we have been reeling under a massive talent crunch for digital technologies. As of 2022, a huge talent war is attracting digital talent across all services, consulting, and product-based companies.
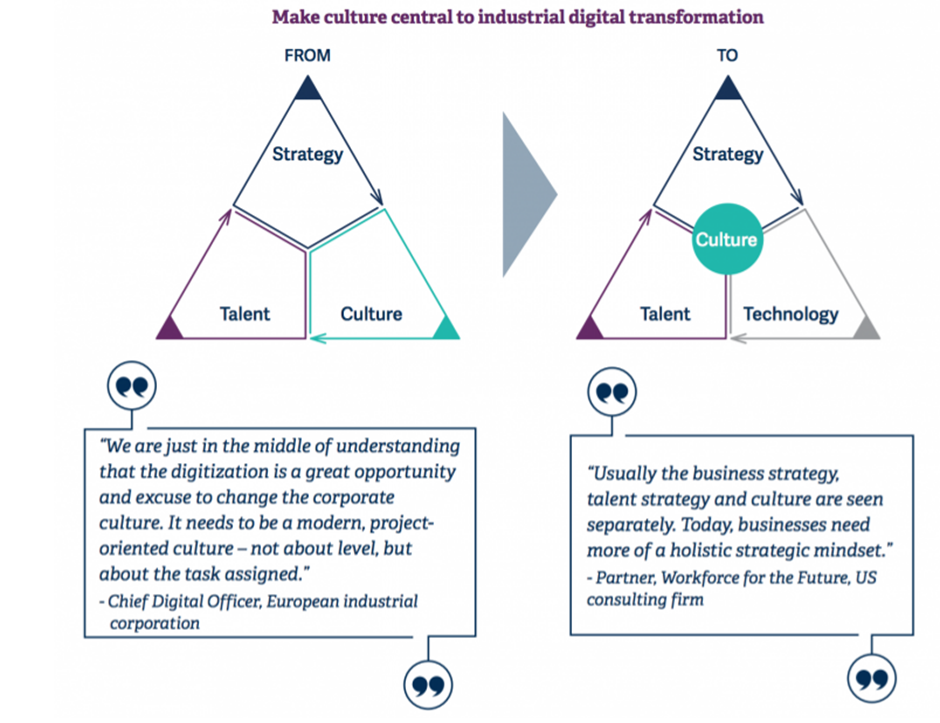
As a result, we don’t have enough people who have seen the actual physical shop floor, understand day-to-day challenges, and have enough digital and technical skills to enable digital transformation. A systematic approach is needed to help up-skill existing resources and develop new digital talent across all levels.
5. CXO Sponsorship:
This is a key foundation for any digital transformation and Industry4.0 initiative. Unless there’s CXO buy-in and sponsorship, any digital transformation initiative is bound to fail. For CXO’s to start believing in the cause, they need to be onboarded, starting with just awareness of what’s possible, emphasizing benefits and ROI as reasons to believe.
Once there’s a top-down willingness and drive, things will become much easier regarding funding, hiring of technical talent or consulting companies, and execution.
Final Takeaway
It should go without saying that the above stats do not include all the challenges manufacturers encounter when they embark on the Industry 4.0 journey. Additionally, more industries and professionals should actively engage in skill improvement initiatives for immediate implementation and prepare employees for the future. Because of the ever-changing nature of IIoT technologies and their rapid pace, this list of challenges will continue to change over time.
We would love to hear back from you on your experiences implementing Industry 4.0 and digital transformation projects and the challenges you faced.
Please feel free to comment and share your experiences.
#Affine is conducting an Event, Demystifying Industry 4.0, on Industry 4.0 and Digital Transformation for CXOs on March 25th, 2022. The Event aims to provide major Industry 4.0 use cases for automotive suppliers and ecosystems.
Stay tuned for more information!
References
[Ref]- https://knowledge.wharton.upenn.edu/article/fedex-digital-transformation/